La automatización está ganando terreno en la manufactura debido a su aportación de eficiencias en los sistemas de producción. Empresas de diferentes sectores están adoptando tecnologías avanzadas para optimizar recursos, mejorar la calidad de los productos y enfrentar desafíos relacionados con los costos y la demanda.
La integración de herramientas como el Internet de las Cosas Industriales (IIoT), la sensorización, la inteligencia artificial (IA), los gemelos digitales y la robótica colaborativa se ha convertido en un eje central para las estrategias operativas.
El Internet de las Cosas Industriales permite a las empresas conectar máquinas y dispositivos en una red inteligente que recopila y analiza datos en tiempo real. Esto posibilita monitorear variables clave en la producción, anticiparse a posibles fallos y tomar decisiones informadas basadas en métricas precisas. Los sensores instalados en líneas de ensamblaje son capaces de identificar patrones anómalos que podrían derivar en fallas mecánicas, permitiendo programar mantenimientos antes de que los problemas afecten la operación.
La inteligencia artificial, por su parte, se ha evidenciado como una herramienta muy útil para gestionar la información generada en las plantas. Los algoritmos diseñados para el análisis de datos pueden optimizar los ciclos de producción, reducir desperdicios y ajustar parámetros de operación en tiempo real. En sectores como la manufactura electrónica, esta tecnología ha demostrado su capacidad para gestionar procesos complejos con altos niveles de precisión, especialmente en la producción de componentes sensibles a variaciones mínimas.
Simular antes de usar recursos
Como parte de esta carrera hacia la automatización, los gemelos digitales se han mostrado como un elemento clave desde el diseño y los proyectos de ingeniería. Estas réplicas virtuales de sistemas físicos permiten simular y analizar diferentes escenarios sin interrumpir las operaciones en el mundo real.
A través de simulaciones, las empresas pueden optimizar diseños, ajustar configuraciones de maquinaria y prever el impacto de cambios operativos antes de implementarlos en el entorno físico. Esto no solo mejora la eficiencia de los procesos, sino que también minimiza riesgos y facilita la planificación estratégica.
Ente los nuevos componentes de la automatización industrial actual también destaca la robótica colaborativa, que ha ganado terreno en plantas donde las tareas manuales requieren un alto grado de precisión o implican riesgos para los operadores.
Los cobots, como se les denomina, están diseñados para trabajar junto con los empleados en una misma estación de trabajo, combinando la capacidad humana para la toma de decisiones con la precisión mecánica. Esto ha permitido reducir tiempos de producción y aumentar la seguridad en sectores como el automotriz y el farmacéutico, donde las normativas demandan altos estándares operativos.
Un detonador en la apuesta en la automatización ha sido la sostenibilidad. Las empresas de manufactura están cada vez más obligadas a buscar la optimización del uso de recursos naturales y así minimizar los residuos generados durante los procesos de producción. La automatización contribuye a estas metas mediante el monitoreo en tiempo real del consumo energético y la identificación de áreas donde se pueden realizar ajustes para reducir el impacto ambiental. En muchas plantas, esto ha llevado a una disminución significativa de costos operativos y una mejora en el cumplimiento de regulaciones internacionales.
Hacia la madurez autómata
La adopción de la automatización no está exenta de desafíos. Las empresas enfrentan barreras relacionadas con el costo inicial de las inversiones necesarias para actualizar equipos e integrar nuevos sistemas. Además, la capacitación del personal es fundamental para asegurar que los operadores puedan gestionar y mantener estas tecnologías de manera adecuada. Otro aspecto crítico es la ciberseguridad, ya que el aumento de la conectividad entre dispositivos y redes industriales incrementa la exposición a amenazas digitales.
A pesar de estas barreras, la tendencia hacia la automatización continúa en ascenso. En mercados globales donde la competitividad depende de la capacidad para adaptarse rápidamente a las demandas cambiantes, las empresas están priorizando la digitalización de sus operaciones. La interoperabilidad entre sistemas y la capacidad de generar datos útiles para la toma de decisiones estratégicas son factores clave que están impulsando esta transición.
En términos de impacto económico, la automatización está cambiando la dinámica del empleo en el sector manufacturero. Si bien algunas tareas repetitivas están siendo reemplazadas por máquinas, se están creando nuevas oportunidades laborales en áreas como el análisis de datos, la programación de sistemas y el mantenimiento avanzado.
Todo lo anterior ha generado una transformación en los perfiles profesionales requeridos por la industria, con una mayor demanda de habilidades técnicas relacionadas con la digitalización y la automatización.
Es posible pensar que estamos ante un punto de inflexión donde la integración de tecnologías avanzadas podría definir la capacidad de una empresa para ser competitivo. Empresas de diferentes tamaños están explorando soluciones adaptadas a sus necesidades específicas, desde pequeñas mejoras en procesos operativos hasta la implementación de sistemas completamente automatizados. A fin de cuentas, la automatización debe ser una transición planificada y estructurada hacia un modelo de producción más eficiente y sostenible.
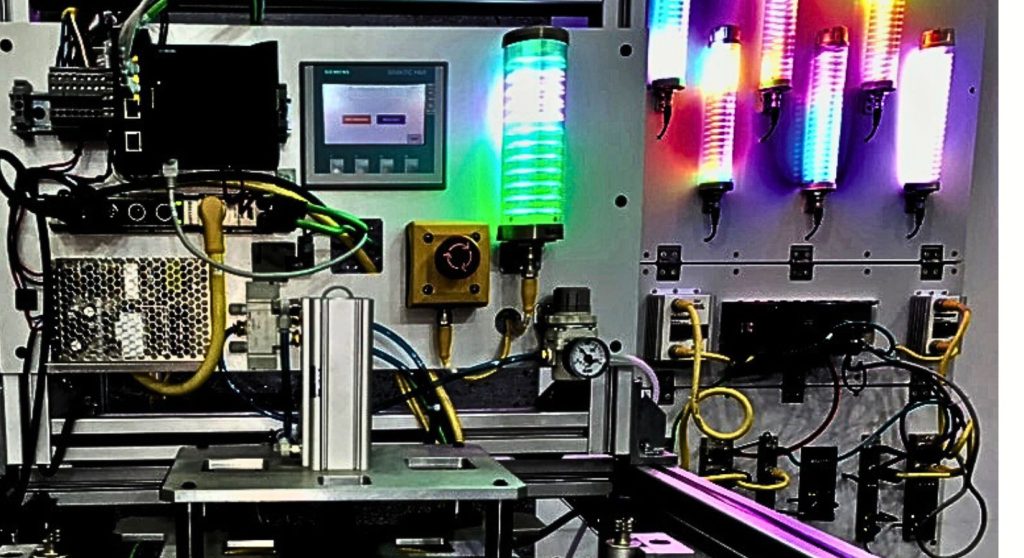